书目名称 | Proceedings of the FISITA 2012 World Automotive Congress | 副标题 | Volume 13: Noise, Vi | 编辑 | SAE-China,FISITA | 视频video | http://file.papertrans.cn/759/758493/758493.mp4 | 概述 | Shows the advanced technologies in automotive industry of the world.The biennial FISITA World Automotive Congress is recognized as the leading international forum for the knowledge exchange in all are | 丛书名称 | Lecture Notes in Electrical Engineering | 图书封面 | 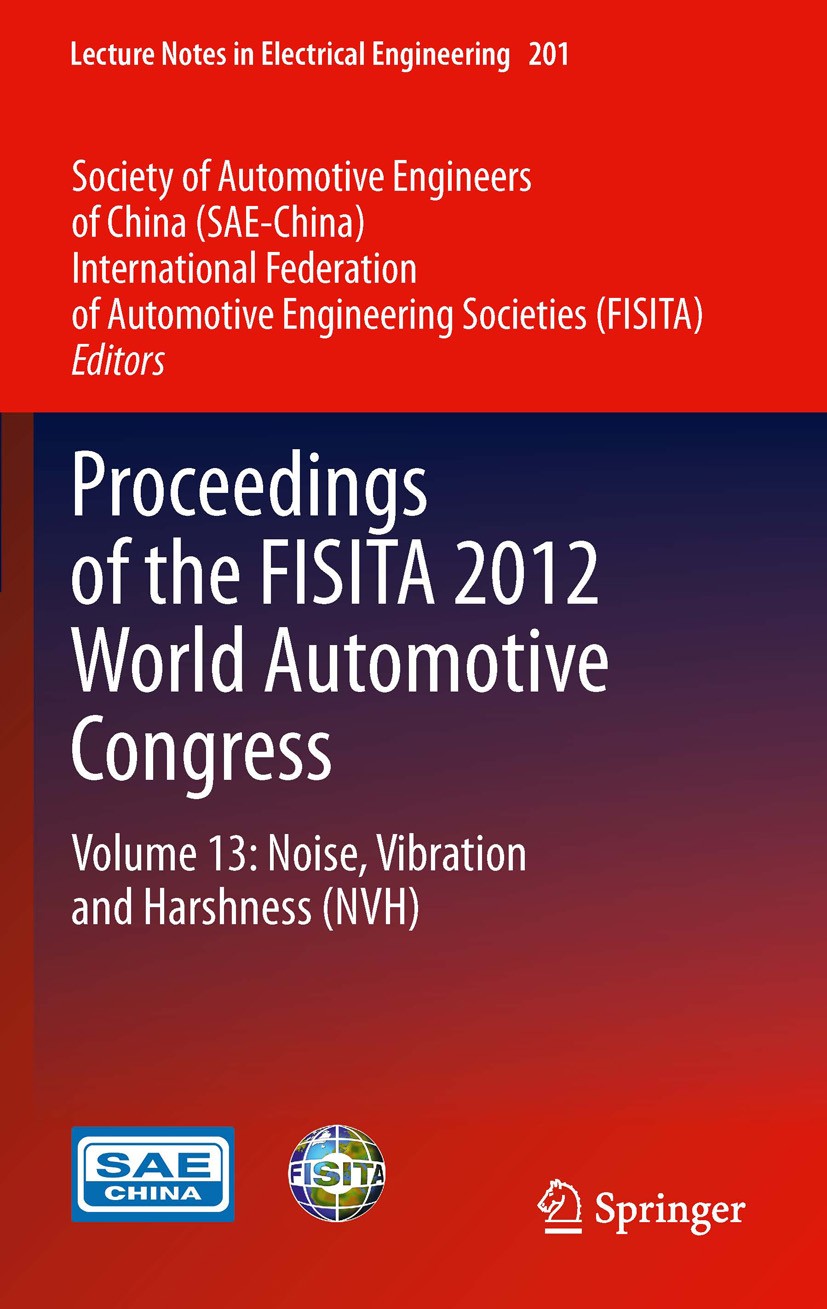 | 描述 | .Proceedings of the FISITA 2012 World Automotive Congress. are selected from nearly 2,000 papers submitted to the 34th FISITA World Automotive Congress, which is held by Society of Automotive Engineers of China (SAE-China ) and the International Federation of Automotive Engineering Societies (FISITA). This proceedings focus on solutions for sustainable mobility in all areas of passenger car, truck and bus transportation. Volume 13: Noise, Vibration and Harshness (NVH) focuses on: .•Chassis Vibration and Noise Control .•Transmission Vibration and Noise Control .•Engine Vibration and Noise Control .•Body Vibration and Noise Control .•Vehicle Vibration and Noise Control .•Analysis and Evaluation of In-Car Vibration & Noise .•Wind Noise Control Technology .•Vibration and Noise Testing Technology .Above all researchers, professional engineers and graduates in fields of automotive engineering, mechanical engineering and electronic engineering will benefit from this book. . .SAE-China is a national academic organization composed of enterprises and professionals who focus on research, design and education in the fields of automotive and related industries. FISITA is the umbrella organizat | 出版日期 | Conference proceedings 2013 | 关键词 | Body Vibration; Chassis Vibration; Engine Vibration; FISITA 2012; In-Car Vibration; Noise Control; Noise, | 版次 | 1 | doi | https://doi.org/10.1007/978-3-642-33832-8 | isbn_softcover | 978-3-662-51146-6 | isbn_ebook | 978-3-642-33832-8Series ISSN 1876-1100 Series E-ISSN 1876-1119 | issn_series | 1876-1100 | copyright | Springer-Verlag Berlin Heidelberg 2013 |
1 |
Parameters Sensitivity Analysis of Self-Excited Vibration of Tires |
Xianwu Yang,Shuguang Zuo |
|
Abstract
To resolve the issues of multi-polygonal wear of tire with high-speed, a multi-dynamic model, considering the four inter-coupling degrees of toe angle, camber angle, vertical vibration and self-excited vibration of tread along with the lateral direction, is built. The model is motivated by the component velocity of vehicle driving speed along with the lateral direction of tire and the sensitivity analysis of parameters, affecting the bifurcation speeds of vehicle, is gained by a numerical simulation method. At the end of this paper, several control strategies with crucial engineering significance are concluded to suppress the self-excited vibration of tire, and then decrease the multi-polygonal ware of tread.
|
2 |
Shimmy Identification Caused by Self-Excitation Components at Vehicle High Speed |
Fujiang Min,Wei Wen,Lifeng Zhao,Xiongying Yu,Jiang Xu |
|
Abstract
The chapter introduces the shimmy mechanism caused by self-excitation components for a vehicle while shimmy is identified at 120 km/h. The Operating Deflection Shape (ODS) analysis used for the chassis from 90 to 140 km/h. The front-right lower arm is identified as the shimmy cause by analysis of movement characteristic change of the chassis components.
|
3 |
Nonlinear Transient Dynamic Analysis of Disc Brake Squeal Using Improved Hilbert-Huang Transform |
Xiandong Liu,Haixia Wang,Yingchun Shan,Tian He |
|
Abstract
Brake squeal is believed as a friction-induced, self-excited phenomenon. The nonlinear transient analysis is the only appropriate method for the brake system with strong nonlinearities. The braking simulation is conducted based on a finite element model of disc brake, and their time–frequency properties of transient and stationary nonlinear response obtained by the improved Hilbert-Huang Transform are presented to investigate the transient dynamic behavior of brake system. It is demonstrated that the dynamic response of the friction-induced vibration is composed of multiple IMF components. The low-frequency IMF components have relative constant instantaneous frequencies but fluctuated energy with time. On the contrary, the high-frequency components have significant fluctuated frequencies. It is considered that the variations of the high-frequency are attributed to the nonlinearity of the brake system that includes the friction damping and contact nonlinearity in the present work. Some higher frequencies appear in the stationary vibration stage after the transient response. The propensity of system instability and brake squeal rises with an increase in friction coefficient. The simulated processing results have also manifested that the improved HHT can clearly provide the time–frequency property of the brake system compared to the conventional HHT, hence, it is a promising tool for processing the complicated nonlinear and nonstationary signals.
|
4 |
Application of an Experimental Tire Model for Comfort Analysis: Requirement for Accurate Low Frequency Tire-Patch Inputs |
Alessandro Lepore,Theo Geluk,Massimiliano Gobbi,Ben Meek |
|
Abstract
Physically correct and invariant inputs are important in vehicle development to perform virtual optimization at the suspension or body-level. These inputs can be applied to vehicle models in order to predict interior vibration or noise-levels and evaluate NVH performances without having a physical prototype. The applied inputs can be wheel-center loads or, even more invariant, tire-patch displacements. These tire-patch inputs, applied to a tire model, allow accurate predictions up to 300 Hz. A limitation of this approach however, is that no accurate inputs can be obtained at lower frequencies, therefore application for comfort analysis is not possible. In this study it is investigated if the low-frequency quality loss in the input identification is related to the measurement approach, the data post-processing steps, or non-linearities in the tire or suspension. An alternative measurement setup including the use of strain-sensors is evaluated and compared with the original acceleration-based methodology. A comparison of predicted target vibrations at the seat rail as well as obtained inputs is presented for the different methods. The results indicate that the proposed alternative methodology increases the quality of the estimated inputs in the low-frequency region. With these improved low-frequency inputs, the methodology of using tire-patch displacements as inputs to hybrid models can now also be applied for lower frequency (ride, comfort) applications.
|
5 |
Torsional Finite Element Analysis of Driveline Torsional Vibration for a Front Wheel Driveline Vehicle Development |
Yuanfeng Xia,Hongcheng Li,Xiong Tian,Hongying Wang,Yu Tang |
|
Abstract
The purpose of this paper is to study the torsional vibration of Front Wheel Driveline (FWD), to avoid the torsional resonance with vehicle, to reduce the torsional vibration and gear rattle noise, and to find out the sensitive factors for controlling the torsional vibration. A torsional finite method is used to establish a 4D-freedom torsional vibration analysis model for FWD system. The natural frequency and modal shapes are calculated, and the torsional vibration characteristics are acquired by system excitation. A 4D-freedom torsional vibration model is established, and numerical simulation for the characteristics of the driveline is analyzed. An optimal method is established to reduce driveline torsional vibration and gear rattle noise. Many factors, such as rotational shaft unbalance, shaft offset its rotation center due to the clearance of universal joints, splines and other components, and non-straight of driveshaft, influence torsional vibration. In order to simplify the analysis model, these factors are not considered. A torsional vibration analysis model with torsional finite method is established, a matching method between system stiffness and damping is presented to reduce driveline torsional vibration and gear rattle noise. In the third order mode of the driveline system, the input shaft of the transmission has the biggest amplitude and its modal frequencies vary with different gears. In order to avoid torsional resonance with other components, the torsional modal frequency could be changed by modulating the stiffness of clutch, driveshaft and tire. The NVH tests show that it’s effective to reduce the torsional vibration by modulating the clutch stiffness and torsional angle.
|
6 |
Transfer Paths Identification and Optimization of Transmission Gear Rattle Noise |
Tian Xiong,Hongcheng Li,Hongying Wang,Yang Xianwu,Yu Tang,Yuanfeng Xia |
|
Abstract
The purpose of this study is to solve the transmission gear rattle phenomenon. The whole vehicle transmission loss (TL) method is used to calculate air-borne rattle noise and to identify if the interior sound is dominated by structure-borne noise and air-borne noise. The major noise transfer paths are found. The experiment analysis indicates that structural transfer paths are identified as the major noise transfer paths for gear rattle noise. The paper provides two ways to improve the transmission gear rattle phenomenon. The test results show the good performance. Some structural transfer paths such as clutch cable, gear shift cables are considered and other factors such as drive half-shafts, suspension systems and subframe system are not considered. All structural transfer path parameters will be considered in the future research.
|
7 |
Study on Driveline Component Torsional Stiffness Effect on RWD Driveline Torsional Vibration Modes |
Qian Zhao |
|
Abstract
As driveline torsional vibration modes are very critical for RWD vehicle NVH issues, like vehicle shuffle, gear rattle, gear/axle whine, and interior noise booming, it is very helpful to find out how driveline component torsinal stiffness affect driveline torsional vibration modes, that make set the torsional vibration mode target much easier from the very start of driveline development and more effectively tune the driveline torsional vibration modes during refine stage, that way, the major goal of this paper is to find out the RWD driveline torsional vibration mode sensibility to driveline component torsional stiffness, in terms of clutch damper, propshaft, axle shaft and rules how to tune the RWD driveline torsional vibration modes to alleviate torsional vibration induced NVH issues. . A RWD SUV driveline lumped mass model is firstly established to predict the 3 most critical torsional modes, then, in-vehicle torsional vibration measurement in this SUV is implemented, and the correlation between the prediction and measurement is judged to decide whether the model can be employed to make driveline torsinal vibration mode sensibility study to driveline component torsional stiffness or not. If the model is accurate, the clutch torsion damper stiffness, propshaft stiffness, axle shaft stiffness are chosen as the parameter, with stiffness increased/decreased 20–80 % compared to original value, to calculate relevant torsional mode for respective component torsional stiffness, hence, the sensibility study can be implemented. . The model prediction correlates very well to the in-vehicle torsional vibration measurement, thus, the model is employed to make driveline torsinal vibration mode sensibility study to driveline component torsional stiffness, as aforementioned way of analysis, to conclude how the driveline component torsional stiffness affect the driveline torsional vibration modes. . This study is only limited to RWD driveline, while, FWD driveline is not covered, hence, the FWD driveline torsional vibration mode sensitivity to driveline component torsional stiffness will be the following study. . This paper involves the systematic study on the driveline component torsional stiffness effect on torsional vibration modes, and give some suggestion addressing the driveline torsional modes from the very start of driveline NVH development, while, the author previous work mainly focused on specific problem solving. In this sense, the work in this paper provides study from new angle. . (1) axle shaft stiffness is the dominant factor for 1st torsinal mode, say vehicle shuffle (2) clutch torsion damper stiffness is the dominant factor for 2nd torsional mode, say gear rattle (3) propshaft stiffness is the dominant factor for 3rd torsional mode, say axle whine (4) the study outcome is beneficial for driveline NVH target setting and tuning direction for vehicle shuffle, gear rattle, axle whine.
|
8 |
Reduction of Structure-Borne Noise by Simulation |
Sabine Sanzenbacher,Bernd Bertsche |
|
Abstract
The main targets in the development of transmissions are increasing driving performance, efficiency and driving comfort. An important aspect in this context is decreasing transmission noise. The most significant transmission noise is whining. It is caused by mesh contact noise of gear pairs under load. The excitations caused by the tooth contact are transferred to the gearbox housing by gearwheel bodies, shafts and bearings. Here from they are either transmitted to the attached parts (by structure-borne noise) or emitted to the environment as air-borne noise. In this paper an approach for the simulation of the noise behaviour of a transmission will be presented. To compute the level of structure-borne noise on the surface of the gearbox housing, a simulation model was built in a multi-body simulation environment. The excitation phenomenon of whining as well as the propagation of the resulting structure-borne noise up to the surface of the housing is considered in this model. Therefore, shafts and housing are integrated in the multi-body simulation as flexible bodies. Additionally, an element to abate propagation of structure-borne noise is introduced. An effective way is to encapsulate the bearings. In this case a ring between the bearing outer ring and the housing is used. Different designs of the rings will be presented as well as their potential to reduce the transmission of structure-borne noise which is estimated in a finite element simulation. To validate the model, measurements of an experimental transmission are made. On a testing bench, a single-stage transmission is driven under specified load and speed. Accelerometers are installed at different positions on the housing and measured results are compared to the simulation results at these positions.
|
9 |
Dynamic Characteristics of Vehicular Planetary Gears Influenced by Engine Excitation and Backlash Based on Nonlinear Torsional Vibration Model |
Hui Liu,Zhongchang Cai,Changle Xiang |
|
Abstract
Multiple gear ratios in automatic transmission are achievable with multi-stage planetary gears, where there are both the loaded planetary gear and the idle planetary gear under some gear ratios operation. Due to the change of road conditions, engine runs with different rotational speed and torque, which brings an external fluctuation excitation to the automatic transmission planetary gear set. In addition, the gear backlash becomes larger with the wear increasing during the running. Both engine excitation and gear backlash are important factors that not only influence the vibration characteristic and meshing state of the loaded planetary gear but also those of the idle planetary gear. The objective of this paper was to investigate the change of meshing force state of loaded planetary gear and idle planetary gear influenced by the different backlash and the engine excitation based on a nonlinear torsional vibration model.
|
10 |
Dynamic Optimization of Vehicle Planetary Transmission Based on GA and FEA |
Changle Xiang,Cheng Wang,Hui Liu,Zhongchang Cai |
|
Abstract
Based on the nonlinear model of vehicle planetary transmission, the dynamic optimization model is established. This work use a combined objective function, internal and external load sharing coefficients and peak-to-peak mesh forces of second stage planetary are taken as objectives. The structure parameters of transmission shafts are considered as design variables. Finite Element Analysis (FEA) is carried out to obtain the bending and torsional stiffness, and the maximal Von-Mises stress constraint. Innovatively, we propose and introduce the nonlinear characteristic constraint aim at increasing the reliability of optimization. The Isight-Matlab-Ansys co-simulation method is applied to build the optimization platform. Finally, the optimization moel of vehicle planetary transmission is solved by Genetic Algorithm (GA).
|
11 |
NVH Optimization of Vehicle Powertrain |
Shouwei Lu,Huihua Feng,Zhengxing Zuo,Liyun Kang,Bo Yu |
|
Abstract
The noise and vibration performance of powertrain is main contributor for vehicle NVH (Noise, Vibration and Harshness) issue. To achieve better NVH performance, it is critical to conduct NVH optimization during the powertrain initial design stage. This paper presents an investigation of optimize vehicle powertrain NVH performance via modification of excitation–radiation system of powertrain. To minimize excitation force of the gearbox with special focus on gear pair dynamic characteristics via the gear profile modification, and to reduce transmission housing noise radiation via enhance its stiffness, are the main objective of optimization. The excitation forces are analyzed by Multi Body Dynamics (MBD) method, considering different excitation mechanisms of the powertrain. The vibro-acoustic behavior of powertrain is obtained by FEM/BEM coupled analysis. The acoustic transfer vector (ATV) calculation is used to predict the powertrain sound power level (SPL) and panel contributions. Based on the acquired NVH data of the powertrain, the optimization which couples the transmission gear profile modification for attenuating gear system excitation and the structure stiffness modification for reducing transmission housing noise radiation is proposed. Experiment validation is conducted in order to evaluate the modified results. The evaluation shows that the optimization can effectively reduce powertrain noise and vibration.
|
12 |
Input Torque Shaping for Driveline NVH Improvement and Torque Profile Approximation Problem with Combustion Pressure |
Kazuhide Togai,Michael Platten |
|
Abstract
The powertrain is the largest excitation source of automotive noise and vibration. Torque variations from the engine cause noise and vibration in two frequency regimes: Engine firing fluctuations at the engine rotation frequency and its harmonics and driver-demanded propulsion torque variations at lower frequencies. This paper examines the mechanisms of gear rattle noise caused by engine firing fluctuations and shock and jerk caused by propulsion torque variations. Gear rattle behaviour is simulated and various approaches for reducing gear rattle are investigated. It is found that isolation of engine firing fluctuations from the transmission is the most effective practical way to reduce rattle. Torque profile shaping by robust control is a method that can be used to reduce shock and jerk. A pre-compensator approach based on knowledge of the driveline resonant properties is proposed and the sensitivity of the controller to errors in the assumed resonant frequencies is investigated. It is shown that one of the constraints of this strategy is that the resolution of control system depends on the firing frequency.
|
13 |
Wheel Load Oriented Control of Semi-Active and Active Suspension Systems Using Pre-Located Road Sampling |
Sebastian Spirk,Kay-Uwe Henning |
|
Abstract
The conflict of objectives in vertical suspension control could be significantly eased by adjusting the settings of stiffness and damping according to the actual driving state. With an adaptive reference model based control emulating a passive suspension with time-varying stiffness and damping coefficient this can be realized using an active or hybrid suspension system. The concept offers huge benefits in comfort for smooth and uncritical excitations. However, in safety critical situations the possibilities for a safety-oriented setting are limited to the dynamic wheel load Pareto-optimal configuration reachable of passive suspensions. Using road profile information, gained by vertically sampling the road underneath the vehicle, a wheel load optimal disturbance compensation can be derived and is applied to a semi-active and hybrid suspension system. Applying this transparent feedforward control law in combination with a reference model based control, dynamic wheel load deviations can be significantly reduced while additionally reducing chassis accelerations.
|
14 |
Optimization of the Range Extender Mounting System for Electric Vehicle |
Yutao Luo,En-ming Lai |
|
Abstract
In this chapter, the mounting system of a range extended electric vehicle is studied. The energy decoupling method and the stiffness matrix method is applied. The optimization calculation of the range extender mounting system is carried out in MATLAB and ADAMS, and the results show that there is good consistency between them. Energy decoupling method is well known to decouple the engine mounting system. The energy distribution of dominant vibration is selected as the objective function under stiffness and natural frequency constraints. The traditional optimal algorithms such as sequential quadratic programming and genetic algorithms are adopted in the energy decoupling optimization for the range extender mounting system. Both optimal coordinates of installation location and best stiffness values are achieved through genetic algorithm method and sequential quadratic programming method. Consequently, the result calculated by genetic algorithm is considered as the final result of energy decoupling method, because genetic algorithm is a global optimum algorithm but sequential quadratic programming is not. The optimum results show that the energy decoupling of genetic algorithms and stiffness matrix method are reliable and accurate. However, the energy decoupling method based on genetic algorithm will be better. A reliable basis is provided for the further optimization design of engine mounting system.
|
15 |
Middle and High Frequency Sound Attenuation Optimization of Air Cleaner |
Liang Yang,Xiaohong Kuang,Shuo Zhang,Haiyan Zhang |
|
Abstract
According to the spectral characteristics of vehicle intake orifice noise, the dominant noise contribution is identified in the range of frequency 800–1200 Hz. Based on the three-dimensional FEM method, the acoustic performance of the air cleaner is studied. The transmission loss of the air filter with additional chamber is improved in middle and high frequency. The acoustic attenuation of the additional chamber is related to the location and structure parameters. By increasing the cross-sectional area and the height of additional chamber, the acoustic attenuation bandwidth and amplitude are improved. Applied this procedure to the optimization of air cleaner structure, the results testified show that the procedure is reasonable and feasible. It can be applied in air cleaner design to increase the middle and high frequency of transmission loss of air intake systems.
|
16 |
NVH Performance Optimization of Cylinder Head in Concept Stage |
Zhanhui Li,Lei Zhang,Xiaoyu Ai,Fengqin Li,Yongjiang Xu |
|
Abstract
Cylinder head with good concept design provides possibility for excellent NVH performance of engine. In order to achieve this, NVH function of cylinder head should be taken into account at concept stage to make sure a good foundation for late stage of engineering. In this chapter, at concept stage of engine development, designs of three different cylinder heads such as global architecture, water jacket, bolt number, bolt position and ribs in different sections are evaluated and compared. In this way, good designs and weaknesses are separated and sorted out in views of NVH. Along with these good designs, one head design of these three is rebuild and recalculated by means of simulation. Results show good NVH improvement of modes and responses and eventually proved the validity of designs. By the research in this chapter, firstly, the NVH performance of production has been improved. Secondly, reasonable structure characteristics of cylinder head are obtained which could be a part of cylinder head design database in view of NVH. And one creditable simulation working flow, by use of mode analysis method and structural attenuation method, for improving cylinder head NVH performance in engine concept development stage is established as well.
|
|
|