书目名称 | Design of Flexible Production Systems | 副标题 | Methodologies and To | 编辑 | Tullio Tolio | 视频video | http://file.papertrans.cn/269/268715/268715.mp4 | 概述 | New approach to design flexible manufacturing system architectures (Focused Flexibility Manufacturing Systems-FFMSs) endowed with the right level of flexibility required by the specific production pro | 图书封面 | 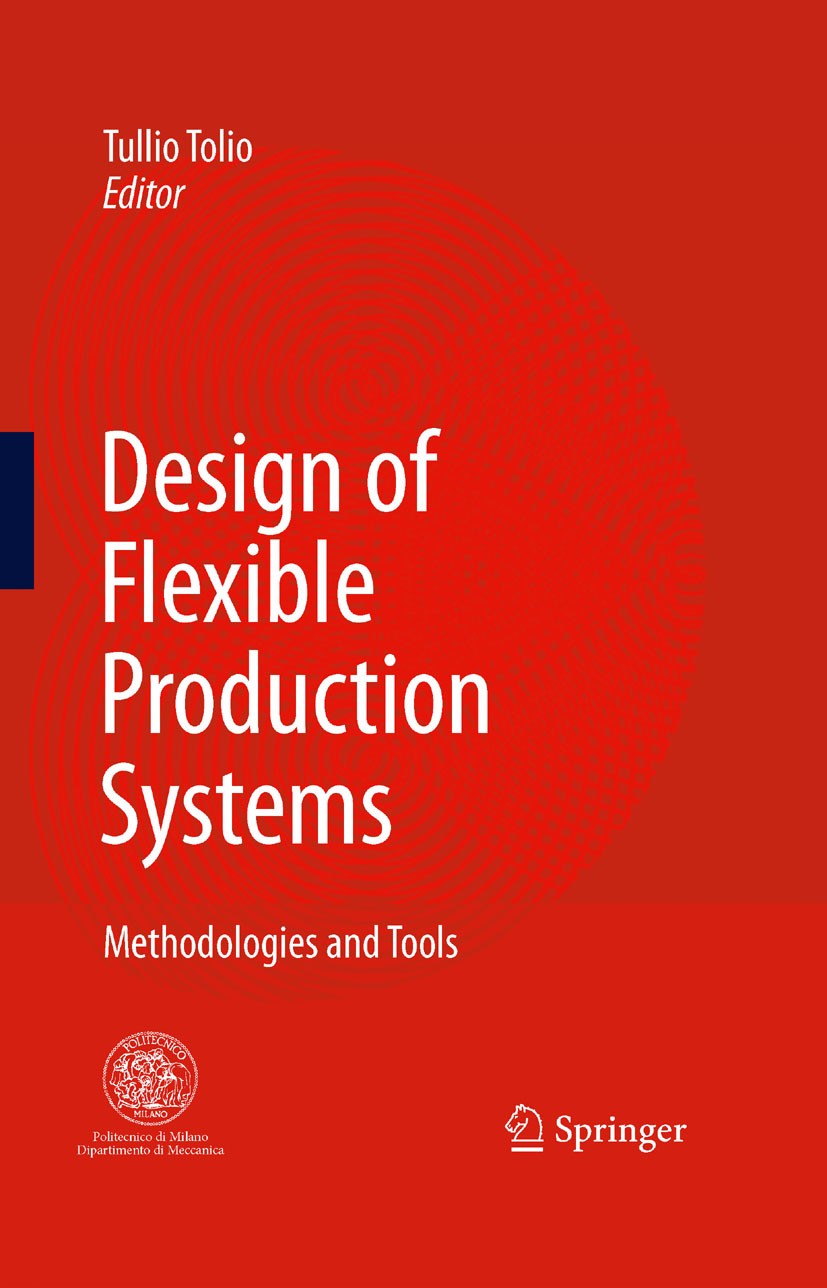 | 描述 | .In the last decade, the production of mechanical components to be assembled in final products produced in high volumes (e.g. cars, mopeds, industrial vehicles, etc.) has undergone deep changes due to the overall modifications in the way companies compete. Companies must consider competitive factors such as short lead times, tight product tolerances, frequent market changes and cost reduction. Anyway, companies often have to define production objectives as trade-offs among these critical factors since it can be difficult to improve all of them...Even if system flexibility is often considered a fundamental requirement for firms, it is not always a desirable characteristic of a system because it requires relevant investment cost which can jeopardize the profitability of the firm. Dedicated systems are not able to adapt to changes of the product characteristics while flexible systems offer more flexibility than what is needed, thus increasing investment and operative costs. Production contexts characterized by mid to high demand volume of well identified families of products in continuous evolution do not require the highest level of flexibility; therefore, manufacturing system flexib | 出版日期 | Book 2009 | 关键词 | Focused Flexibilty; Manufacturing Strategy; Manufacturing System; Manufacturing System Design; Manufactu | 版次 | 1 | doi | https://doi.org/10.1007/978-3-540-85414-2 | isbn_softcover | 978-3-642-09908-3 | isbn_ebook | 978-3-540-85414-2 | copyright | Springer-Verlag Berlin Heidelberg 2009 |
The information of publication is updating
|
|